New moving 3D printing platform-
“Researchers have created a low-cost reusable support method to reduce the need for 3-D printers to print wasteful supports, vastly improving cost-effectiveness and sustainability for 3-D printing.“
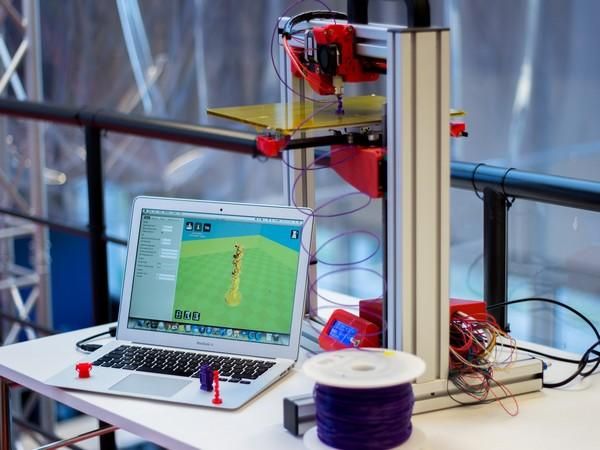
The following written content by University of Southern California
3-D printing has the potential to revolutionize product design and manufacturing in a vast range of fields — from custom components for consumer products, to 3-D printed dental products and bone and medical implants that could save lives.
However, the process also creates a large amount of expensive and unsustainable waste and takes a long time, making it difficult for 3-D printing to be implemented on a wide scale.
Each time a 3-D printer produces custom objects, especially unusually-shaped products, it also needs to print supports-printed stands that balance the object as the printer creates layer by layer, helping maintain its shape integrity. However, these supports must be manually removed after printing, which requires finishing by hand and can result in shape inaccuracies or surface roughness. The materials the supports are made from often cannot be re-used, and so they’re discarded, contributing to the growing problem of 3-D printed waste material.
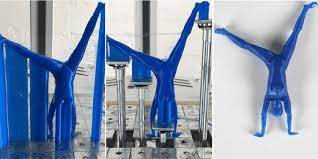
For the first time, researchers in USC Viterbi’s Daniel J. Epstein Department of Industrial and Systems Engineering have created a low-cost reusable support method to reduce the need for 3-D printers to print these wasteful supports, vastly improving cost-effectiveness and sustainability for 3-D printing.
The work, led by Yong Chen, professor of industrial and systems engineering and PhD student Yang Xu, has been published in Additive Manufacturing.
Traditional 3-D printing using the Fused Deposition Modeling (FDM) technique, prints layer-by-layer, directly onto a static metal surface. The new prototype instead uses a programmable, dynamically-controlled surface made of moveable metal pins to replace the printed supports. The pins rise up as the printer progressively builds the product. Chen said that testing of the new prototype has shown it saves around 35% in materials used to print objects. Read more from Science Daily.